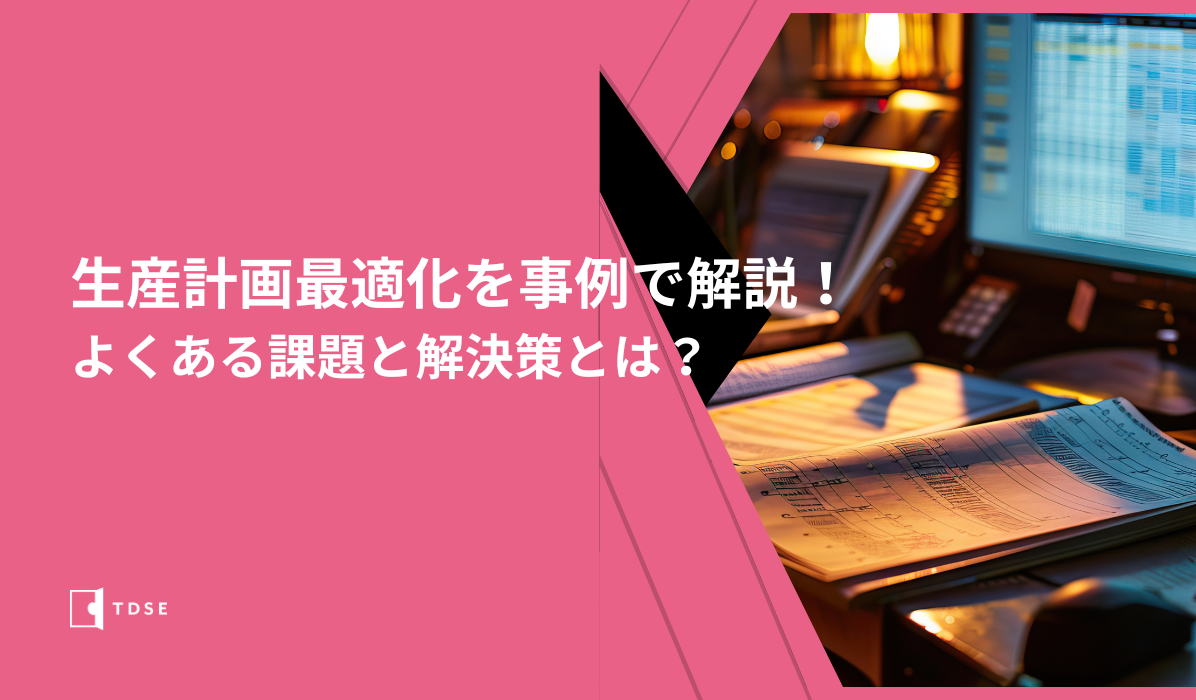
目次
生産計画における課題
生産計画によくある問題
生産計画は、「どの製品をどのくらい、いつまでに生産するか」を決定する、製造業務においてたいへん重要な業務です。
こちらの記事もぜひご覧ください。
▶生産計画最適化とは?生産計画にAI・数理最適化を導入する3つのメリットを解説!
▶生産計画を数理最適化問題として解く!現場実装のための業務要件に合わせたチューニングとは?
生産計画を策定する業務において、以下のような問題を抱えている現場は多いのではないでしょうか。
- ・計画策定に要する時間の長期化
- ・計画業務の属人化
- ・状況の変化に伴う計画精度の低下
生産計画の策定には、部品や原材料の入荷状況や設備の稼働状況など、複雑な条件を考慮する必要があります。特に多品種少量生産の場合は、実用に足る計画を策定するのに考慮すべき条件が多く、多くの時間がかかります。
また、計画業務では複雑な条件を考慮する必要があるため、知識や経験が特定の担当者に偏る属人化が進んでしまうケースも多いと思います。属人化が進んでしまうと、担当者不在時の対応が難しくなったり、担当者によって計画の精度にばらつきが発生したりする事態も起こります。
さらに、生産計画は、製品の需要などの市場動向の変化や、設備の故障、顧客からの納期の変更要求など、さまざまな状況の変化に応じて修正・変更していく必要があります。これらの変化に柔軟に対応できないと、納期遅れの発生や在庫の過不足の発生など、企業の損失につながってしまいます。
生産計画のデジタル化
こういった問題を解決するために、生産計画にAI・数理最適化を導入することに注目が集まっています。AIを活用することで、生産計画の業務効率化・生産性向上などが期待できますが、まずは生産計画に必要なデータの整備が必須となります。つまり、製品生産に必要なリソースがいつ・どのくらい必要になるかを明確化し、デジタル化する必要があります。特に、製品生産に必要なリソースを、4M(Man, Machine, Method, Material)、つまり人・設備・手順・原材料の観点で洗い出し、明確化します。
- 人:生産ラインを回すために必要な人員の数や求められる技術・工数など
- 設備:生産設備の構成や数量、稼働時間など
- 手順:加工・組立・運搬などの作業方法や作業の順番、設備の操作方法など
- 原材料:製品の生産に必要な原材料や部品の種類や数量、規格、使用するタイミングなど
また、納期の変更などの状況の変化に対応していくためには、計画を見直す際に常に最新かつ正確なデータにアクセスできるよう、データ基盤の仕様を設計するように注意する必要があります。
生産計画への数理最適化・AI導入事例
ここまで、生産計画における問題や課題について解説してきました。ここからは、生産計画へAI・数理最適化を導入し、課題の解決に寄与した事例をいくつかご紹介します。
事例①生産拠点の最適化(小売)
まずは、商品をどの工場で生産するかを決定する計画業務に数理最適化を導入した事例をご紹介します。
課題 | 人手での計画策定に多くの時間を要し、生産計画の練り直しに伴った手戻りが発生していた |
---|---|
解決策 | 商品の生産コストや輸送コスト、各工場の生産能力などの各種条件を整理し、これをもとに生産計画業務を数理最適化問題として定式化し、最適化モデルを実装 |
効果 | 自動で生産計画を策定できるようになり、生産計画にかかる工数の大幅な削減や、計画業務の属人化の解消 |
この事例では、「どの商品を、どの工場で、どれだけ、いつまでに生産するか」の生産計画を人手で実施していたお客様の業務において、数理最適化を導入しました。この事例の計画業務では、季節によって需要が異なるため生産すべき商品が変わったり、各地の工場で生産できる商品も様々であったりなど、複雑な条件を考慮する必要があり、人手で計画を策定するのに多くの時間を要していました。また、状況の変化に伴い計画通りの生産ができなくなってしまった場合、担当者の方は計画を練り直す必要があり、手戻りが発生するという課題もありました。
その課題を解決するため、生産計画に必要な商品の生産コストや輸送コスト、各工場の生産能力などの各種条件を整理し、これをもとに生産計画業務を数理最適化問題として定式化し、最適化モデルを実装しました。最適化モデルを業務フローに導入することで、自動で生産計画を策定できるようになり、生産計画にかかる工数の大幅な削減や、計画業務の属人化の解消が期待できます。
事例②生産工程における不具合要因分析(鉄鋼)
次に、生産計画にAIを導入した事例をご紹介します。
課題 | 生産工程における不具合原因の特定をしたい。 不具合要因の特定に基づいて生産計画の見直しを行い、生産性を向上させたい |
---|---|
解決策 | 生産工程における不具合の直接的な要因および間接的な要因をAI予測モデルから特徴として抽出し、どのファクターの影響が大きいかを割り出す |
効果 | これまで特定できなかった不具合要因を特定することができるようになり、要因に応じて生産計画の見直しを行うことで、生産効率が向上した |
この事例では、AIを活用することで、製品の生産工程における不具合要因を特定しました。具体的には、生産工程における不具合の直接的な要因および間接的な要因をAI予測モデルから特徴として抽出し、どのファクターの影響が大きいかを割り出しました。これにより、これまで特定できなかった不具合要因を特定することができるようになり、要因に応じて生産計画の見直しを行うことで、生産効率の向上が可能となります。
まとめ
ここまで、生産計画における課題と、生産計画へのAI・数理最適化の導入事例についてご紹介しました。
導入事例はほんの一部であり、お客様の業務の状況に応じて、計画策定時に考慮すべき各種条件を柔軟に変更し、生産計画を最適化することが可能です。また、AIによる予測や可視化を併せて活用することで、さらなる生産効率向上が期待できます。このようなメリットを享受するには、生産計画に必要な情報をデジタル化することが第一ステップとなります。
特に製造業は堅固な組織文化や、拠点間、工程間のデータ連携の難しさがAI導入の大きな壁となるケースも多くあります。
まずはスモールステップでAIに対する信頼感を高めていくような取り組みから始める必要もあるかもしれません。
TDSEでは、これまで多くの製造業のお客様のデータ利活用によるDX推進をご支援してまいりました。
生産計画の最適化、AI導入にもしご興味をお持ちでしたら、ぜひお気軽にご相談、お問い合わせください!TDSEの専門チームが、お客様の具体的なニーズに合わせたソリューションをご提案いたします。